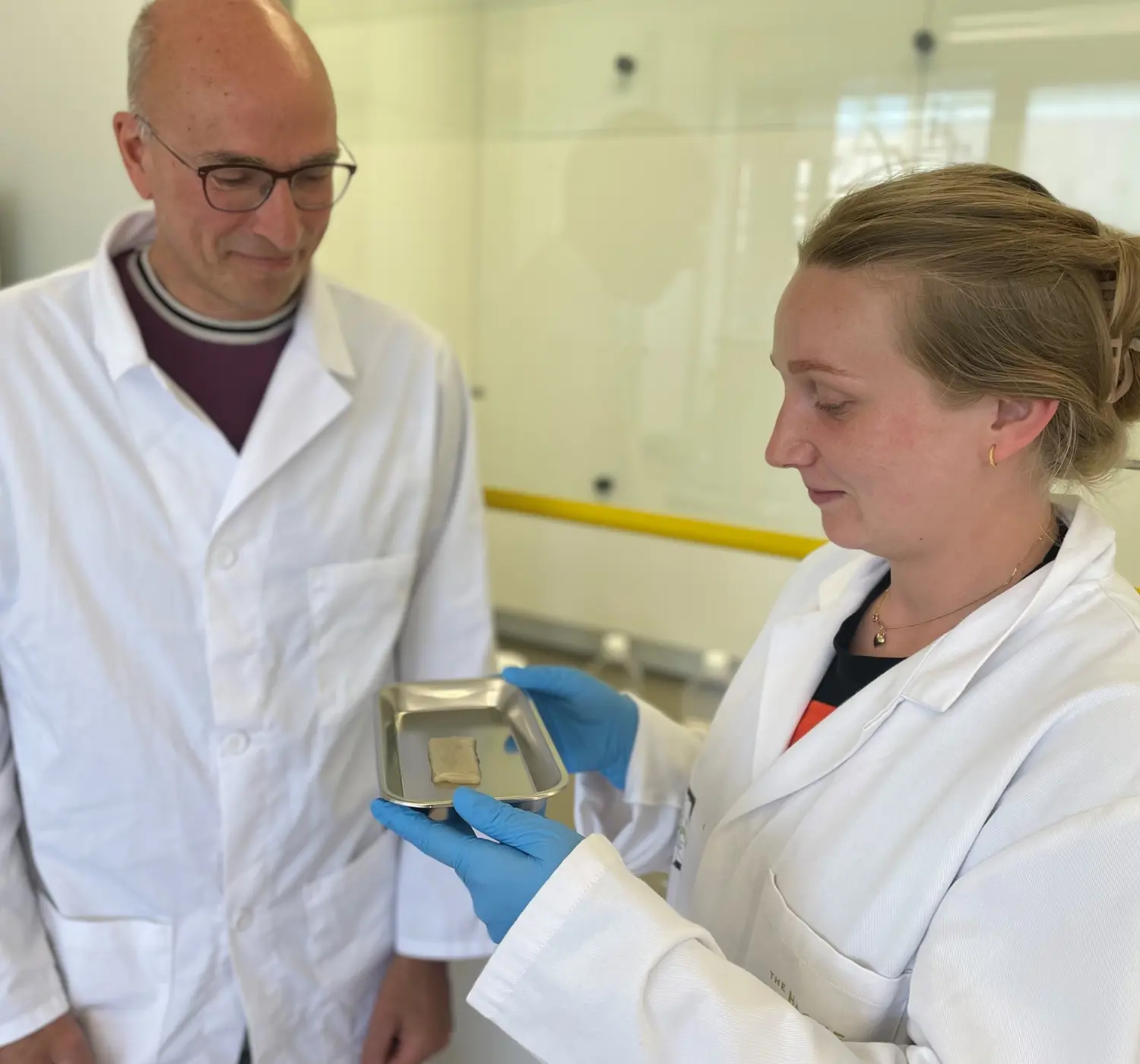
Every year the world produces enough polystyrene - commonly known as Styrofoam - to cover the size of Manhattan. This material, which takes over 500 years to decompose, continues to accumulate with no end in sight. This alarming reality is what drives Foamlab, a groundbreaking startup on a mission to replace this pollutive substance with a sustainable, compostable alternative. By tackling one of the most common environmental challenges of our time, Foamlab is ready to revolutionize the future of materials.
“Foamlab is focused on offering compostable alternatives for Styrofoam or polystyrene," says Jeroen van Rotterdam, co-founder of Foamlab. "Styrofoam is extremely pollutive. What we're trying to do is create an alternative that is compostable at room temperature and under natural environments, which is crucial because a lot of bioplastics require high temperatures to break down.”
Foamlab’s expertise lies in the complex integration of science, design, and engineering - a combination they believe is crucial for achieving their ambitious goals.
The science behind Foamlab
Born from groundbreaking research at the Technical University of Delft (TU Delft), the innovation driving Foamlab stems from bacterial nanocellulose, a material that Jeroen describes as "a platform for materials" due to its versatility. Bacterial nanocellulose is produced by bacteria that consume glucose and create a polymer, which can then be modified to enhance specific material properties. "We know how to produce the material and how to tweak its properties," Jeroen explains. "But there's a big difference between lab scale and production scale, and that’s what we’re working on here at Planet B.io—mimicking a mini production site and figuring out how to scale."
Despite being a startup of only three weeks old, the team behind Foamlab is deeply committed to transforming this innovation into a market-ready product. They’re not only focusing on scaling production but also on identifying the best applications for their foam. "We are navigating the space, looking for a beachhead market," says Jeroen. "Ideally, we want to go for something that is low volume and high gross margin, but we’re also considering high-volume, lower-margin applications like packaging."
Challenges and opportunities
Scaling production is one of the most significant challenges facing Foamlab. The polystyrene market is enormous - valued at $29 billion annually and growing. "This is an impact startup," Jeroen notes. "We want to change the trajectory for the environment, and that comes with volume. But it's hard to develop the required production environment."
Foamlab is not alone in the bioplastics arena, but their focus on foam derived from bacterial cellulose gives them a unique edge. "There are bioplastics companies focused on foam, but I’m not aware of anyone producing foam based on bacterial cellulose," Jeroen explains. "Our material has a huge tensile strength, much stronger than polystyrene, which leads to potential applications that polystyrene cannot handle."
"Our material has a huge tensile strength, much stronger than polystyrene, which leads to potential applications that polystyrene cannot handle."
A strategic path forward
Jeroen’s approach to launching Foamlab is deeply informed by his past entrepreneurial experiences. He emphasizes the importance of selecting the right target market early on. "In a startup, it’s crucial to focus your efforts towards a certain application in a target market," he says. "If you have stamina and stick with a topic long enough, you will figure it out."
One particularly promising market is aerospace, where the demand for strong, lightweight materials could align perfectly with Foamlab’s foam. Medical applications too, are a possibility, given the pure, skin-friendly nature of bacterial cellulose. However, Jeroen remains pragmatic: "It's all about finding a market where the unique properties of our material give us an edge, allowing us to enter with a high price point and high gross margin."
Building the future at Planet B.io
Foamlab’s residence at Planet B.io is a strategic move. The startup community and the lab facilities at Planet B.io provide Foamlab with the resources it needs to scale up efficiently. Jeroen highlights the importance of the support and expertise within the ecosystem, from potential investor introductions to navigating the complex subsidy landscape.
Looking ahead, Jeroen envisions a model of distributed production, aiming to minimize the environmental impact not just through their material but through the entire production and logistics chain. "We will have a model for production," Jeroen says, imagining a future where production sites are located near customers to reduce transportation costs and environmental footprint. "The challenge with foam is that if you're shipping it around, you're shipping 99% air. We're trying to avoid that."
A vision for impact
Ultimately, Foamlab is driven by the desire to make a significant environmental impact. While the company is still in its early stages, Jeroen's vision is clear: to disrupt the polystyrene market and offer a viable, sustainable alternative. "For me, it's about impact," he says. "If selling the technology creates a bigger impact than producing it ourselves, we'll do that. But for now, we’re focused on bringing this material to market and making a real difference."